Fabulous Prefabs
Save money with an upscale dwelling that arrives on a truck and goes up fast.
Scott and Lisa McGlasson love canoeing, their two sons enjoy fishing for walleyes, and their daughter likes catching fireflies. To indulge their pursuits, each summer the family would bolt from their Minneapolis home to rented cabins at Little Pequaywan Lake, in northern Minnesota.
In 2003 the McGlassons bought a half-acre lot on the lake to build their dream getaway. The couple wanted to keep a lid on building costs, but they did not want to sacrifice great design and solid construction. They met both goals with a two-story modern built by Alchemy Architects, in St. Paul. "During the day we have a lake view from 8-foot windows," says Scott. "But when we close the curtains at night, the living room is chic enough to feel like a New York City apartment."
Row 0 - Cell 0 | Fabulous Prefabs |
Row 1 - Cell 0 | Slide Show: Ten Upscale Prefab Homes |
Row 2 - Cell 0 | Where to Buy Upscale Prefabs |
Row 3 - Cell 0 | Search for the Best Mortgage Rates |
The McGlassons' hideaway -- with two bedrooms, one bathroom and tons of personality -- is a prefabricated home. The components were assembled in a factory, trucked to their lot and put together. But forget double-wides and trailer parks. Today's prefabs are going upscale.
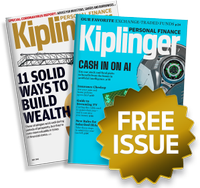
Sign up for Kiplinger’s Free E-Newsletters
Profit and prosper with the best of expert advice on investing, taxes, retirement, personal finance and more - straight to your e-mail.
Profit and prosper with the best of expert advice - straight to your e-mail.
A number of architectural firms now design the homes, then either partner with a prefab manufacturer or have their own factories build them. The homes are meant to be petite and low-maintenance, making them ideal for vacation retreats -- although buyers often choose to add a basement or a second story, raising the houses out of the cottage class.
Upscale prefabs generally run $120 to $300 per square foot, including all costs, from the foundation to the paint on the walls. That's 20% to 30% less than you'd pay for houses custom-designed by architects and built conventionally, although such prefabs are more expensive than mass-produced suburban tract-type houses. Second homes tend to be custom built because buyers want their vacation retreats to have unique, stylish designs -- with features such as the right angles and floor-to-ceiling windows of the mid-century modern style -- that builders of tract-type houses rarely sell. Most upscale prefabs showcase this modern style, giving them a custom-built appearance.
Scott and Lisa paid $95,000 for their second home. They chose the layout of the first story from a half-dozen of Alchemy Architects' plans and added a second story to the blueprints, expanding the size to 780 square feet. The firm hired a Wisconsin factory to manufacture the house's components, a process that took about six weeks. The components were trucked from the factory on a flatbed, and a crane helped assemble them (delivery and crane costs ran $6,000). The McGlassons hired contractors to connect the house's wiring to the electrical grid, dig a well and do other finishing work. The final tally was about $160,000, including fixtures and appliances.
Skittish about the sturdiness of a prefab home? That's a reasonable worry given how trailer parks fare in tornadoes. But the prefab makers cited in this story either build to meet local building codes, or build houses that meet the codes in all of the states in which they sell, making the houses at least as sturdy as conventional ones. For example, the firm Rocio Romero's LV150 home can withstand 150-mile-per-hour winds. Other firms, such as Michelle Kaufmann Designs, sell models that are up to code for use in California's earthquake alley.
Here's the lowdown on the two major styles of upscale prefab homes: panelized and modular. We also offer tips on picking your architectural firm, builder and bank.
Most adaptable
Panelized houses are made of sections stuffed with wiring and insulation. The panels are trucked to your lot, where contractors hired by you (or less commonly, by the prefab firm) join them together. Panelized houses tend to cost more than modular ones. But because the panels can be arranged in different ways, panelized houses can have custom options.
For example, Charlie Lazor, owner of the architectural firm Lazor Office, says that panelized houses can be more intimately integrated into the landscape of your lot. "Our panelized houses can turn corners, take on L-shapes or U-shapes, or step down steep hills," he says. Modular construction doesn't offer that flexibility and generally requires a flat, roomy foundation. The flexibility of a panelized house makes it superior for building on mountain, beach and lakefront locations, which tend to have more quirks than the typical suburban lot.
With a few exceptions, a panelized home runs between $300,000 and $450,000 for a 1,500-square-foot house -- including delivery, construction of a foundation and finishing work.
[page break]
Among upscale prefab homes, the most affordable ones are generally modular and are built in units of entire rooms or larger. Alchemy Architects, Michelle Kaufmann Designs and Office of Mobile Design charge roughly $125,000 to $175,000 for a 1,000-square-foot modular house. You'll pay about the same amount to finish the house.
The major limitation of modular houses is size: Modular units must be able to travel down highways. "We have to do a lot of thinking within the box," jokes Joseph Tanney, a partner at Resolution: 4 Architecture, a New York firm that builds prefab homes using modular and other methods. What's more, modular houses often need thicker-than-usual interior walls to ensure that they will withstand the stress of being lifted onto your lot by a crane. (Panelized homes don't face this problem.) These thicker walls reduce the number of floor plans because there are only so many ways the fatter walls can be disguised.
Caveats aside, the lower costs of modular homes trump other factors for many buyers. Scott McGlasson says that it was the prefab's low cost that made their lakefront home a savvy real estate investment. Adds Lisa: "It's so nice to own an investment we can enjoy."
See our directory of architectural firms and builders to find out where to buy an upscale prefabricated home.
Key decisions
Although the prefab components come at a set price, you may still confront overruns at the site. The amount of finishing work left undone varies by architectural firm and builder. For example, Empyrean International offers a general contractor to oversee construction, including the management of subcontractors to do your electrical, heating and flooring work. Empyrean charges between $175 and $275 per square foot for a completed NextHouse, one of its top models. At the minimalist end of the prefab spectrum, Rocio Romero produces the shell of your house for about $29 per square foot, leaving it to you to hire contractors to finish the job at a further cost of about $120 per square foot.
Finding a contractor to assemble a prefab home can be an issue. Some won't take what they consider small-potatoes projects. Also, when they learn you're building a second home, contractors may hike their prices because they assume you're rich. "Say 'second home' and contractors smell money," notes Michael Buchanan, who built an upscale modular home in Berkshire, N.Y.
To minimize hassles, try having as much of your house finished in the factory as possible. Buchanan, who wrote about his experience in PreFab Home (Gibbs Smith, $25), wishes he had stuck with the standard interior and exterior details offered by his manufacturer, Simplex, instead of hiring contractors to install his own design elements. His 3,800-square-foot house (not including the basement) had a factory cost of about $375,000, with $275,000 more in on-site finishing costs.
Second-home loans
Unlike mortgages for existing homes, prefab homes require construction loans. With this type of loan, the bank parcels out money in stages, sending inspectors at each stage to certify that the work has been done as claimed. Interest rates for these interest-only loans were recently about 1.3 percentage points higher than the average for 30-year fixed-rate mortgages, says Don Taylor, of Bankrate.com.
Don't be penny-wise and pound-foolish. Paying a slight premium to receive financing through a bank that has a specialized department for prefab (also called systems-built or factory-built) houses is generally worth it, says Chris Condon, author of Building Real Estate Riches (McGraw-Hill, $17). Banks familiar with prefab projects, such as Indymac and MT Mortgage, are less likely to disrupt ongoing construction than are other banks. Banks unfamiliar with prefab projects may not be readily willing to pay the large deposit of up to 75% of the loan that prefab factories often require up front.
The most common financing is the construction-to-permanent loan, which converts to a conventional mortgage once your home is completed. This type of loan has an advantage: You face only one closing process and one set of fees. But the loan often comes with fewer repayment options than a conventional mortgage.
Another choice is to start with a construction-only loan and then get a loan with different terms after the construction is finished. Interest rates will be about the same as for a construction-to-permanent loan. This process adds fees and a second closing, but you may get better loan features because you will be able to shop for your mortgage from any bank instead of just the construction-loan specialist.
Next: See our slide show of ten upscale prefabricated homes
Profit and prosper with the best of Kiplinger's advice on investing, taxes, retirement, personal finance and much more. Delivered daily. Enter your email in the box and click Sign Me Up.
-
4 Money Habits Boomers Swore By That Millennials Are Walking Away From
Millennials are trading tradition for flexibility when it comes to building wealth.
-
Abu Dhabi Adventures: New Thrills, Iconic Sights and Disney’s Latest Park
Discover the mix of culture, wildlife and modern marvels that make this Middle Eastern city a destination to watch.
-
How to Search For Foreclosures Near You: Best Websites for Listings
Making Your Money Last Searching for a foreclosed home? These top-rated foreclosure websites — including free, paid and government options — can help you find listings near you.
-
Luxury Home Prices Rise as the Rich Dodge High Mortgage Rates
Luxury home prices rose 9% to the highest third-quarter level on record, Redfin reports, growing nearly three times faster than non-luxury prices.
-
Four Tips for Renting Out Your Home on Airbnb
real estate Here's what you should know before listing your home on Airbnb.
-
Five Ways to Shop for a Low Mortgage Rate
Becoming a Homeowner Mortgage rates are high this year, but you can still find an affordable loan with these tips.
-
Looking to Relocate? Plan for Climate Change
buying a home Extreme weather events are on the rise. If you’re moving, make sure your new home is protected from climate change disasters.
-
Retirees, A Healthy Condo Has a Flush Reserve Fund
Smart Buying Reserve funds for a third of homeowner and condo associations have insufficient cash, experts say. Here are some cautionary steps you should take.
-
Cash Home Buyers: New Services Offer Help Making All-Cash Offers
Becoming a Homeowner Some firms help home buyers make all-cash offers on homes. Weigh the fees before you sign on.
-
Home Sale Prices in the 50 Largest Metro Areas
Becoming a Homeowner What’s happening in the market where you live?