Lighter Vehicles Spell Better Gas Mileage
Steel, aluminum and composite makers are vying to get more of their materials into cars and trucks.
The next car you buy will probably be lighter, courtesy of federal mandates to increase average gas mileage by 30% to 40% over the next five years. Automakers figure the easiest and cheapest way to cut fuel consumption is to make passenger cars, which now weigh about 3,500 pounds on average, about 400 pounds lighter.
Under Uncle Sam’s new rules, the current 27.5 miles per gallon minimum for passenger cars will jump to 33.8 mpg for 2012 models and 39.5 mpg for 2016 models. A similar phased-in approach for light trucks will require them to average 29.8 mpg for 2016 models.
The upshot: Heated competition between steel and aluminum manufacturers for a larger slice of the lucrative pie. Aluminum makers have a weighty advantage and are aiming to use it to muscle out steel for use in vehicle roofs and other body panels, engines and structural components.
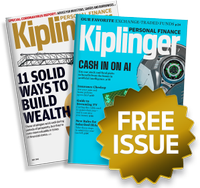
Sign up for Kiplinger’s Free E-Newsletters
Profit and prosper with the best of expert advice on investing, taxes, retirement, personal finance and more - straight to your e-mail.
Profit and prosper with the best of expert advice - straight to your e-mail.
Manufacturers such as Alcoa, Rio Tinto Alcan and Novelis are developing aluminum products with greater strength to better stand up to the everyday dings that cars pick up in parking lots and elsewhere, as well as specialty versions for use in bumpers that crumple to absorb the force of a collision. The aluminum industry is honing its strategy to win a large chunk of the plug-in electric car market that will take off within five years.
Steelmakers are fighting back with a lighter generation of high-strength steel.Thanks to research stretching back 20 years, automotive steel today weighs around 25% less than it did during the heyday of muscle cars in the 1960s and 1970s. Automakers including Ford routinely use this steel in key structural components in auto body pillars and panels.
Now steelmakers are on the cusp of commercializing a breakthrough product that is not only 10% lighter yet, but stronger and more easily molded. “This third-generation product will enable us to make auto parts that are much lighter than today because the steel can be made thinner with no compromise in strength,” says Ronald Krupitzer, a vice president for automotive applications with the American Iron and Steel Institute, a trade group.
Down the road, look for steel and aluminum to be challenged by an even-lighter-weight contender -- composite carbon fiber. Long used in aerospace and for pricey bicycles and tennis rackets, the pricey material has been finding its way into exotic cars such as Chevrolet’s Corvette ZR-1.
Odds are the price differential between carbon fiber and aluminum and steel will narrow by decade’s end, thanks in part to research and development at the Department of Energy’s laboratory in Oak Ridge, Tenn., and at Magna International, Canada’s largest automotive parts supplier.
Profit and prosper with the best of Kiplinger's advice on investing, taxes, retirement, personal finance and much more. Delivered daily. Enter your email in the box and click Sign Me Up.
-
Nvidia Earnings: Live Updates and Commentary August 2025
Nvidia's earnings event is just days away, and market participants are zeroed in on the AI bellwether's quarterly results.
-
Ten Cheapest Places to Live in Tennessee
Property Tax Moving to Tennessee might be within your reach. Homeowners in these counties pay some of the lowest property tax bills in the state.
-
Kiplinger Special Report: Business Costs for 2026
Economic Forecasts Fresh forecasts for 2026, to help you plan ahead and prepare a budget on a range of business costs, from Kiplinger's Letters team.
-
Trump-Era Regulations Will Broaden Access to Crypto
The Kiplinger Letter The president wants to make the U.S. the leader in digital assets.
-
How to Adopt AI and Keep Employees Happy
The Kiplinger Letter As business adoption of AI picks up, employee morale could take a hit. But there are ways to avoid an AI backlash.
-
The Rise of AI: A Kiplinger Special Report
The Kiplinger Letter Our special report looks at the opportunities and challenges of generative AI and how its rapid move into the mainstream is impacting every aspect of our lives.
-
Big Changes Are Ahead for Higher Ed
The Kiplinger Letter A major reform of higher ed is underway. Colleges are bracing for abrupt change, financial headwinds and uncertainty.
-
AI-Powered Smart Glasses Set to Make a Bigger Splash
The Kiplinger Letter Meta leads the way with its sleek, fashionable smart glasses, but Apple reportedly plans to join the fray by late 2026. Improved AI will lure more customers.
-
Breaking China's Stranglehold on Rare Earth Elements
The Letter China is using its near-monopoly on critical minerals to win trade concessions. Can the U.S. find alternate supplies?
-
Things that Surprise Business Owners When It’s Time to Sell
The Kiplinger Letter When it’s time to retire and enjoy the fruits of growing their business, owners are often surprised by how tough it is to give up their baby!